At Custom Case Group, our cases are designed to be fully customizable from start to finish in order to meet your specific requirements.
Through each step of the creation of your case — from the initial concept and design to prototyping and manufacturing — you will be in the driver’s seat. Read more about each phase of the production process below.
Concept
We begin the process by asking questions about your needs — how the case will be used, your budget, the quantity of cases required, special environmental or MIL-SPEC requirements, your timeline for project completion, and any other important factors.
Design
With the initial concept for your case in place, the process then moves into the design phase. In this step, we will ask you for any CAD files of your equipment or have you provide us with access to the equipment itself to take precise measurements.
Approval
After your case design has been finalized, it is presented to you for your approval. Any specific changes that may be required or requested for your case's design will then be added to a revised design before the process proceeds to the next stage.
Prototype
Depending on the quantity of cases or complexity of the design, a first article prototype case may be produced. We will produce a single case in order to verify all of the specific details before proceeding with producing the balance of your order.
Manufacturing
Once final approval of the design and any potential prototype is given, your case is then moved into the manufacturing phase, and it is fully brought to life. All of the case components are assembled, inspected, packaged, and made ready for shipment.
Shipment
When the production of your order is completed, your case is then prepared for shipment and given to a specified carrier and sent on its way to you. As with each step of the process, specific care is taken to ensure your order's quality and accuracy.
MATERIAL Options
Plastic
Plastic cases are either injection-molded or thermoformed from rugged, durable plastic. Plastic custom cases are often watertight, and can be made crushproof and shockproof. They can be made airtight and pressure-regulated, and can conform to a wide range of standards and certifications.
At our factories in California and Minnesota, we customize plastic cases with custom foam interiors, mounting hardware, and other customization options.
While plastic cases are manufactured in thousands of sizes, developing custom sizes of plastic cases is usually cost-prohibitive in all but the largest quantities.
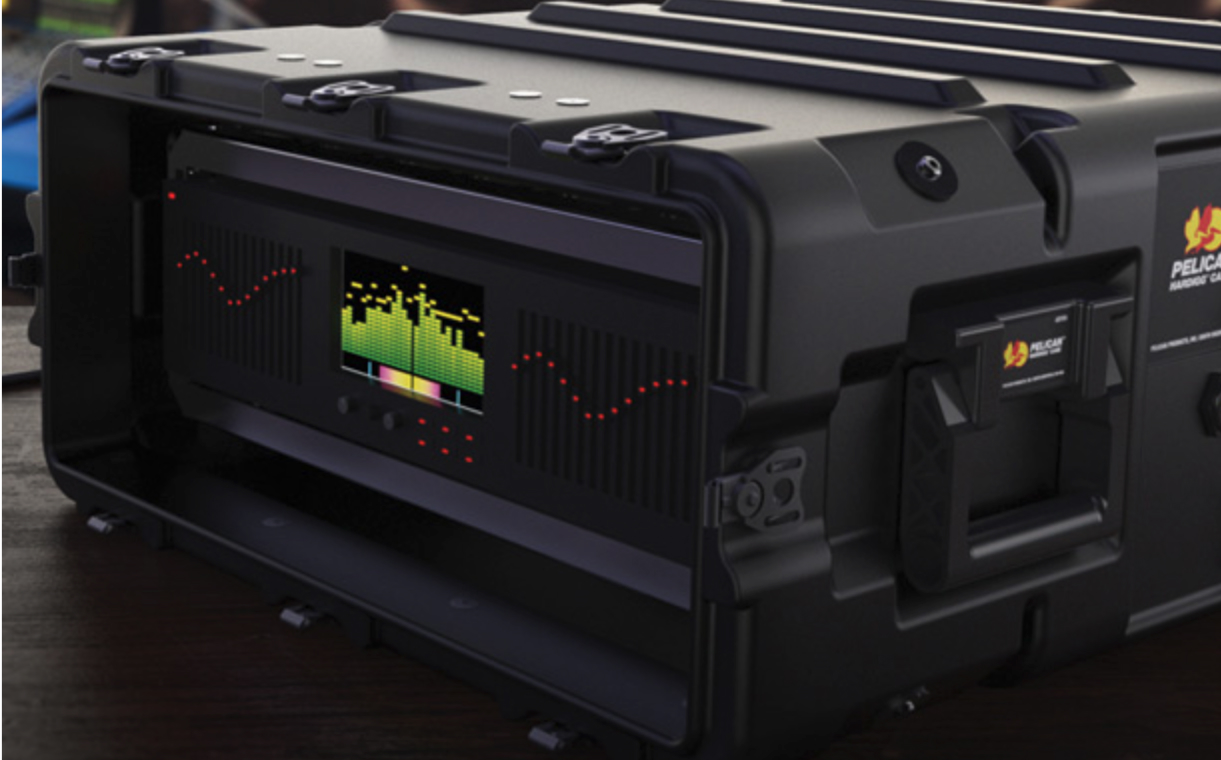
PLASTIC CUSTOMIZATION OPTIONS
Interior
- Custom Foam
- Brackets
- Racks
- Drawers
- Guitar Hangers
- Keyboard Trays
- Nets
- Trays
- Straps
- Shock-Mounting
- Dividers
- Inserts
- Interior Case Ramps
Exterior
- Hardware
- Routings & Holes
- Forklift Skids
- Graphic Wraps
- Locks
- Powder Coating
- Recessed Telescoping
- Handles
- Labels & Logos
- Wheels & Casters
Aluminum
Aluminum custom cases offer a wide range of benefits. Like wood/composite cases, they can be made in completely custom sizes without tooling charges. Like plastic cases, they can be made waterproof and sealed against environmental conditions.
Aluminum is the ideal metal for manufacturing custom cases. It’s lightweight and very robust, while still being a comparatively affordable metal. It’s resistant to corrosion and UV radiation, and fully recyclable.
Our custom aluminum cases are being put to use around the world in a wide range of military, aerospace, industrial, outdoor, and medical applications.
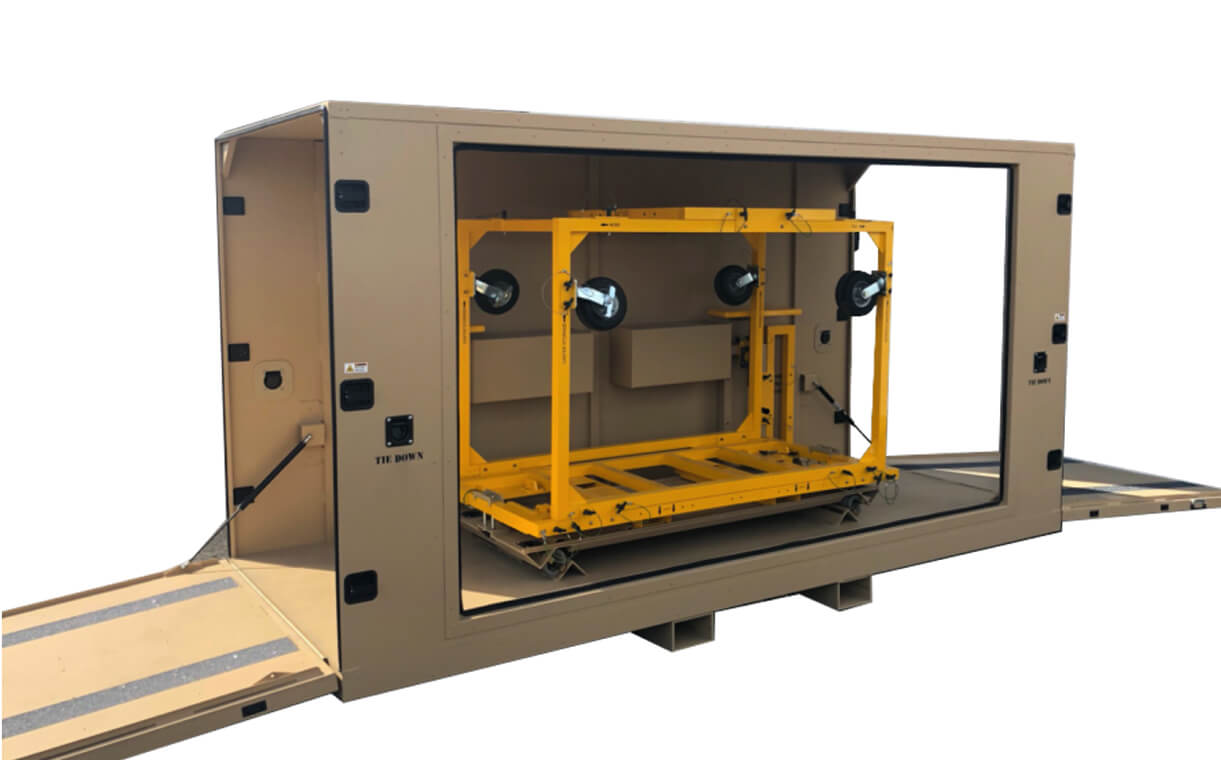
ALUMINUM CUSTOMIZATION OPTIONS
Interior
- Custom Foam
- Brackets
- Racks
- Drawers
- Nets
- Trays
- Straps
- Shock-Mounting
- Dividers
- Inserts
Exterior
- Hardware
- Routings & Holes
- EMI/RF Shielding
- Locks
- I/O Panels
- Custom Reinforcements
- Labels & Logos
- Wheels & Casters
Wood/Composite
Wood/composite cases are made from a combination of materials. Typically, the case’s walls and structural elements are made from an ABS, fiberglass, or aluminum laminate along with ACX or other high-grade plywood. The case’s corners and hinges are made from aluminum and joined with rivets and high-grade hinges.
Wood/composite custom cases can be manufactured in many custom sizes at low, medium, or high quantities. We partner with leading wood/composite custom case manufacturers to offer custom sizes, then complete the customization process at our factories in California and Minnesota.
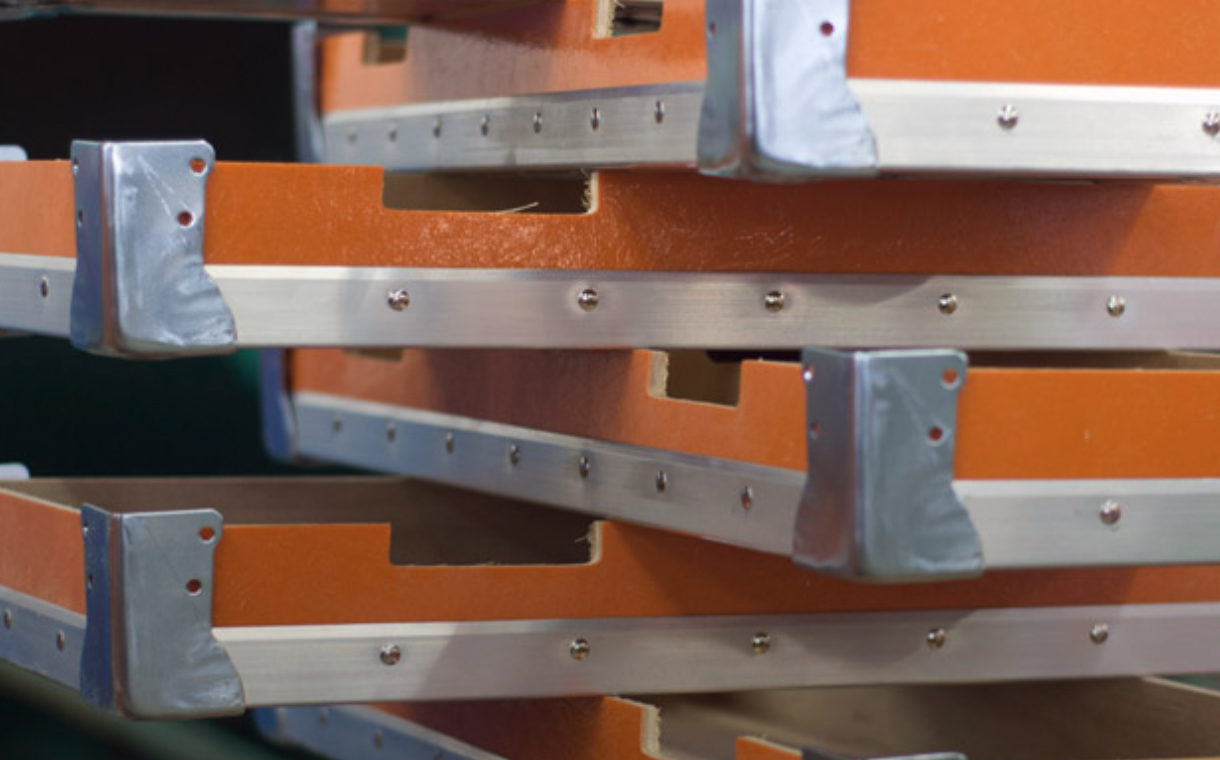
WOOD/COMPOSITE CUSTOMIZATION OPTIONS
Interior
- Custom Foam
- Brackets
- Racks
- Drawers
- Nets
- Trays
- Straps
- Shock-Mounting
- Dividers
- Inserts
Exterior
- Hardware
- Routings & Holes
- EMI/RF Shielding
- Locks
- I/O Panels
- Custom Reinforcements
- Labels & Logos
- Wheels & Casters
Custom Branding
No customization process would be complete without the ability to make your case truly yours by incorporating your custom branding into the case’s look and feel. Your case doesn’t just protect your product — it also advertises your brand. From logos and labels to colors and name plates, we’ll ensure your case is a true representation of your brand.
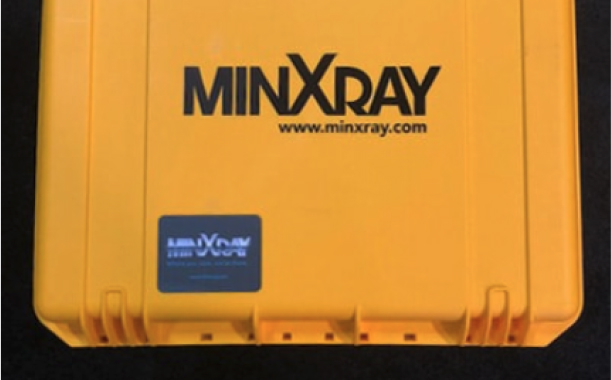
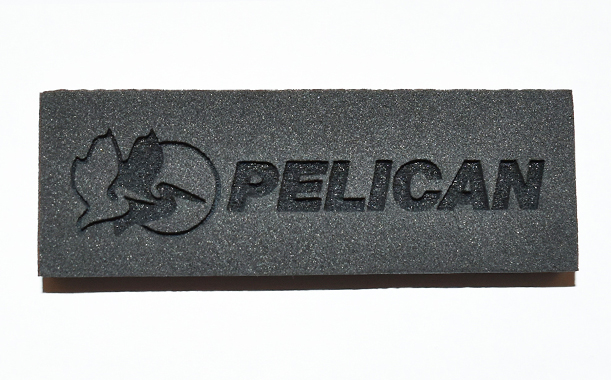
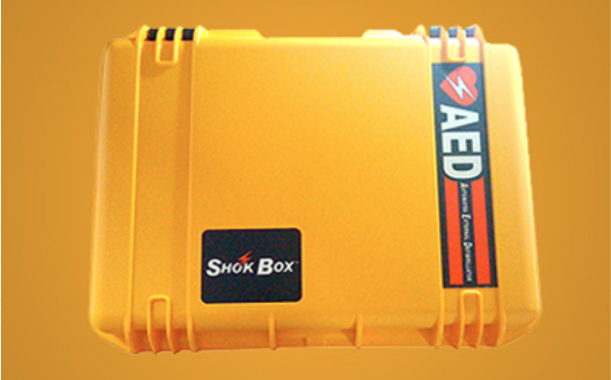
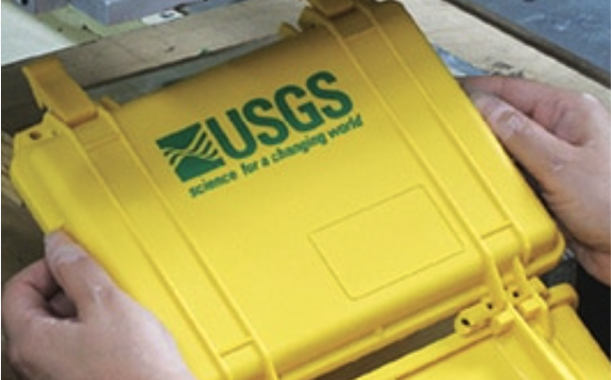
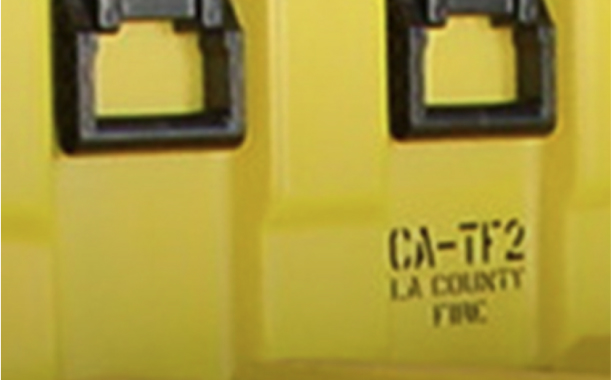
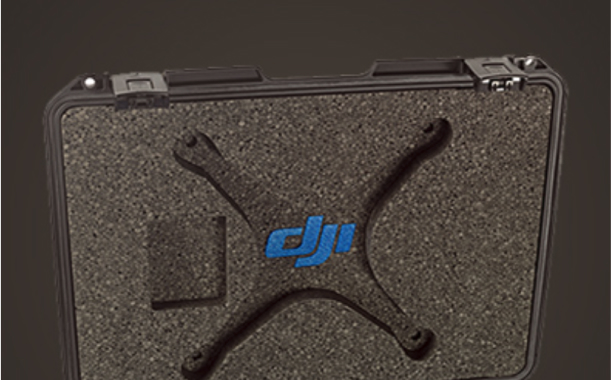
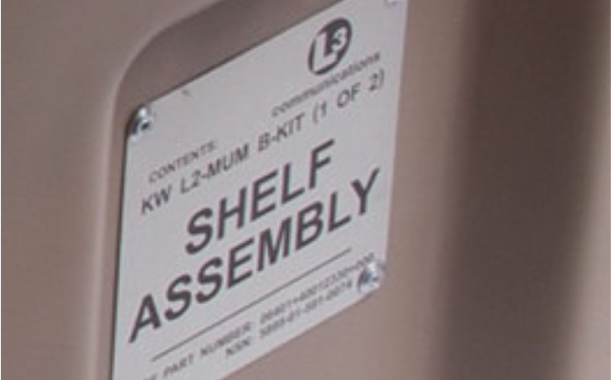

OUR BRANDING OFFERINGS INCLUDE:
- Custom Lexan or vinyl labels
- Laser-etched name plates
- Waterjet-cut logos in foam
- Color-coded handles & latches
- Stencils
- UID labels
- Hot-stamped foil imprints
- Silk screening
Custom Foam
At Custom Case Group, we make custom cases that safely cradle everything from sensitive electronic equipment to rugged tools. How do we accomplish this? Part of the secret is the foam we use to customize the interior of our cases to secure their contents. Depending on the application, we use a variety of methods to deliver customized foam interiors.
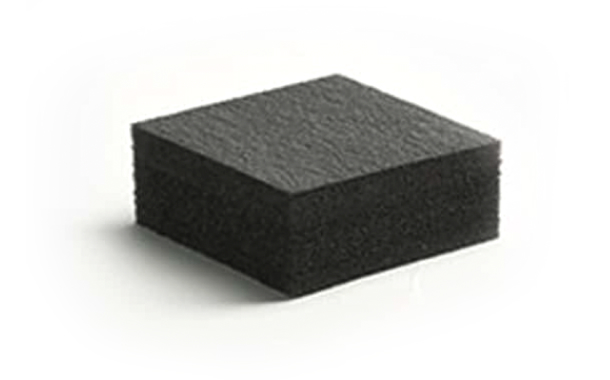

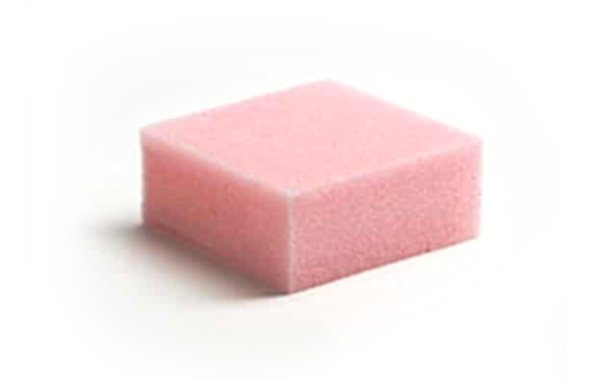
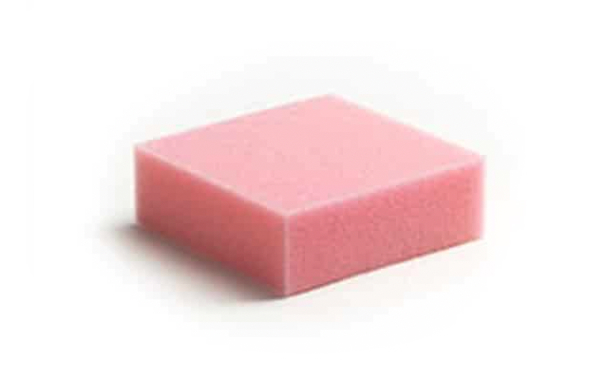
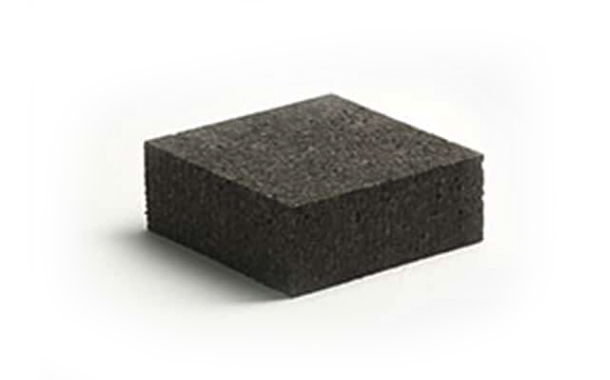
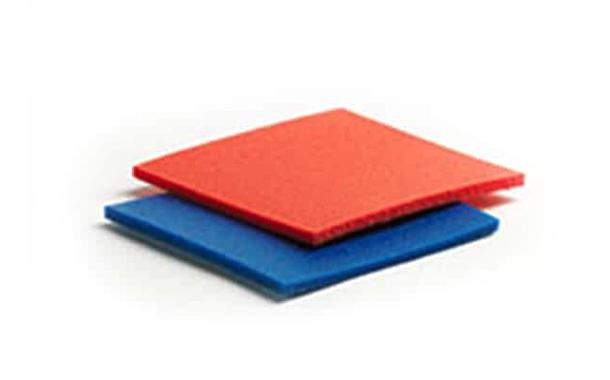
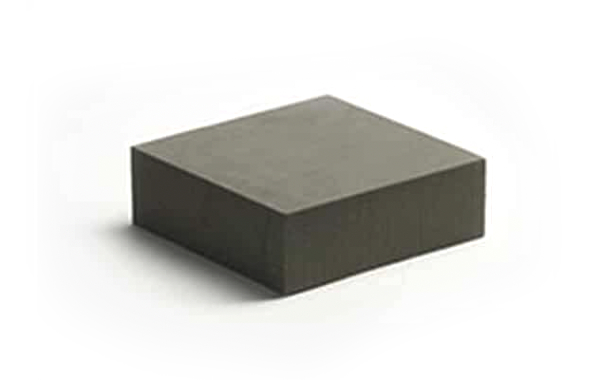
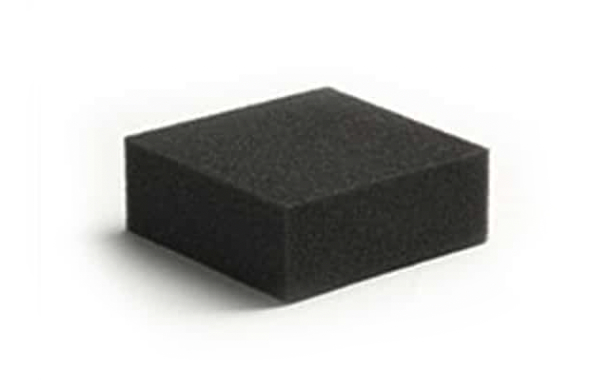
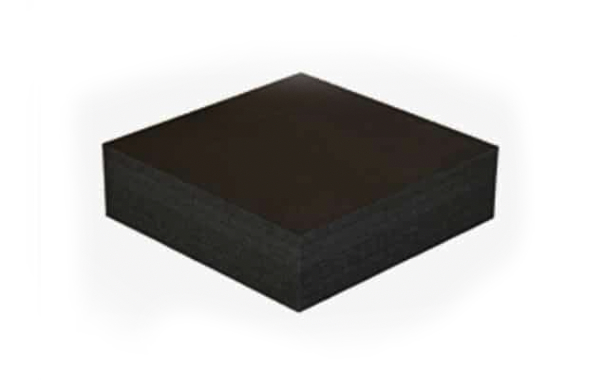
FREQUENTLY ASKED QUESTIONS
Can cases be airtight/watertight?
The Pelican Storm, Air, and Protector line are airtight/watertight as standard.
Pelican-Hardigg Roto Molded Single-Lid, Rack Mount, and Impact aluminum cases can be made airtight/watertight as an option. This option includes a contiguous gasket as well as a pressure relief valve (PRV). These cases can also be fitted with a humidity indicator to indicate internal humidity within the case as well.
Wilson cases unfortunately cannot be made airtight or watertight.
Do cases come in different colors?
Pelican Storm, Air, and Protector cases come standard in Black. Olive Drab Green, Desert Tan, Orange, Yellow, and Silver are also available, but there may be minimum quantities required.
Pelican-Hardigg Roto Molded Single-Lid, and Rack Mount cases come standard in Gray. There are 13 other colors available: Black, White, Red, Light Blue, Dark Blue, Light Yellow, Dark Yellow, Maroon, and Purple.
Impact aluminum cases are available in Mill finish (aluminum) or can be powder-coated in virtually any color for an extra charge.
Wilson cases are available in Blue, Black, Red, and White.
What should I consider when trying to select a case of my items?
How will it be used? Shipped, hand-carried, or wheeled?
Are there size and weight restrictions?
Are the items delicate or sensitive?
Are the items static-sensitive?
How do you select the case size and type?
Once we have all your information, we would make suggestions backed by our knowledge of shipping, storage, and handling. We would never choose a solution based on the highest price to make a larger profit.
We want to provide the best possible solution based on performance and meeting your needs.
Do cases meet Military Specifications?
We have many choices that meet and exceed certain MIL-SPECS. Let us know your requirements, and we’ll guide you to the proper case type and style.
Can I have a logo and/or label added to my case?
All the injection-molded cases (Protector, Storm, and Air) have the ability to do “hot stamped” logos on the lids of the cases. There are minimum quantities that must be met. There are also setup charges and tool creation charges that must be considered. A hi-res image of the artwork is also required.
All the cases can have aftermarket labels added to them. There are setup charges and minimum quantities required, but they are much lower than the “hot stamp” version.
All the injection-molded cases (Protector, Storm, and Air) have a defined, recessed area on the lid.
Dimensions can be provided.
What can be done to make it easy to travel with my case?
Several cases can have edge-mounted casters and retractable handles options, which can be added to them.
What can be done to my case to make it more suitable to handle the rigors of shipping?
Several cases can have “removable casters” added to them. These can be taken off before placed in a truck for transport. We can also add aluminum “Bash Plates” to the lower portion of the case to protect against errant forklift penetration damage.
What can be done to the inside of the case to protect my valuable contents?
We evaluate how fragile an item is going into the case and adjust the type and amount of cushioning material used to encapsulate the item during transit. If proper protection cannot be achieved with cushioning material, we would suggest a metal deck platform suspended by elastomeric shock mounts that protect an item against shock and vibration regardless of the altitude of the item during shipment.
What are the warranties of the different cases?
Each manufacturer warrants their product differently. All warrant against defect in material and workmanship for at least one year. The injection-molded cases (Protector, Storm, and Air) will provide replacement hardware at no charge. None of the manufacturers warrant against damage to the case. The case is there to protect the contents of the case from damage. Scuffs, scrapes, and scratches are going to happen. If you find your case extremely damaged during a shipment, we recommend that you enter a claim against the carrier for that damage. Be certain that you make a note on any documentation associated with the shipment before the driver leaves. Most carriers will deny a damage claim if made after a case has been delivered without notation. At that point, it can’t be determined where and when the damage occurred.
How long does it take to make a case?
It depends on the complexity of the case and cushioning system. It can be as short as a week or two; the more complex cases can take up to 12–14 weeks to produce based on the amount of engineering and materials used in the case solution to best protect your item.
Can the cases have removable lids?
Most can, except Protector, Storm, and Air, which are only available with a hinged lid. All others can have a removable lid and may have choices as to how tall the lid and base can be, based on the requirements and weight of the item going into the case.
Can the cases be locked?
All of the injection-molded cases (Protector, Storm, and Air) come standard with padlock provisions. Other cases have different padlock-able options available.
What happens if I break a handle, latch, or caster?
Most of the hardware on the plastic cases are field-replaceable and require minimal hand tools to exchange the parts. Hardware on the Wilson and Impact cases are riveted in place but can still be replaced with a little work by drilling out rivets or replacing fasteners.
Can the cases be reconfigured to fit other items?
Most of the interiors are produced as a free-standing cushion that is tacked or mechanically held in place, making them easier to repurpose.
Do the airlines have size restrictions for overhead and checked baggage?
Yes, they do. The dimensions and weights are ever-changing. We recommend that you contact your carrier for the specifics of their requirements.